Direct-to-film (DTF) printing is a game-changer in the world of custom apparel. Unlike traditional methods like screen printing or direct-to-garment (DTG) printing, DTF lets you apply high-quality, full-color transfers to a wide range of fabrics — including cotton, polyester, blends, and even non-textile surfaces. This printing process eliminates the need for fabric pretreatment and produces crisp, vibrant, and highly durable designs.
DTF printing offers unmatched flexibility and efficiency for businesses. Whether you’re a small custom print shop, a growing e-commerce brand, or a large-scale apparel manufacturer, DTF provides a cost-effective way to create detailed, multi-color prints with minimal setup time. It also enables print-on-demand fulfillment, helping businesses scale their operations without large inventory maintenance.
Want to achieve optimal results? Understanding the key terms associated with DTF transfers is crucial. From choosing the right adhesive powder to preventing ink from clogging your printer, mastering DTF terminology empowers you to troubleshoot issues, optimize production, and maximize the quality of your prints. This glossary is designed to be your go-to reference guide, helping you navigate the world of DTF printing with confidence and clarity.
Glossary of Direct-to-Film (DTF) Transfer Terms

DTF Printing Process Terms
DTF printing follows a specific process to ensure high-quality, durable, and vibrant prints. Each step plays a crucial role in producing results that meet industry standards. From the initial design to the final transfer, these terms will help you understand the fundamentals of DTF printing.
Direct to Film (DTF) Printing
DTF is a heat transfer printing method where designs are digitally printed onto a special PET film. The film is coated with adhesive powder, cured, and then heat-pressed onto fabric. This method produces high-quality, detailed prints that can be applied to garments using heat and pressure.
Unlike DTG or screen printing, DTF works on cotton, polyester, blends, and more — without pretreatment.
Direct-to-Garment (DTG) Printing
DTG is a textile printing method in which a garment (usually pre-treated) is printed directly using specialized inkjet inks without a transfer film. The DTG method prints directly onto the fabric (often cotton). It also typically requires a pretreatment step for dark garments to effectively bond the ink.
Screen Printing
Screen printing is a traditional printing technique in which ink is pushed through a mesh stencil (screen) onto the garment. Each color requires a separate screen, making it best for bulk runs. Screen printing creates durable designs but involves more setup than digital methods like DTF.
Gang Sheet
A gang sheet is a layout technique where multiple designs are printed on one large transfer sheet. This maximizes the efficient use of film and powder.
Gang sheets are ideal for bulk orders. They reduce waste and cut costs per print since many images share the same sheet.
Heat Transfer Vinyl (HTV)
HTV is a decoration method where cut vinyl material is applied to a garment using a heat press.
Designs are cut from colored vinyl sheets (or printed on special vinyl) and then pressed onto fabric; HTV comes in many styles (solid colors, glitter, flock, etc.) and is popular for its durability.
Sublimation Printing
Sublimation printing is a technique in which special dyes are printed onto paper and then heated to sublimate (turn into gas), bonding with polyester fabric fibers. This printing process embeds the ink into the garment for a vibrant, permanent design, but it works best on high-polyester-content materials.
Pretreatment
Pretreatment is when a preparatory coating is applied to garments (especially dark shirts) before DTG or other specific transfers to help inks bond and colors pop. The pretreatment is usually heat-pressed to flatten fibers. This creates a smooth, receptive surface for printing.
Unlike DTG, DTF transfers do not require garment pretreatment because the adhesive powder provides the bond.
Underbase (White Ink Layer)
An underbase is a foundation layer of white ink that is printed before any colored ink to ensure opacity on dark fabrics. It is also sometimes called a white ink layer.
Without an underbase, colors can appear muted or transparent on non-white garments.
Curing
Curing is the process of melting and setting the adhesive powder on a DTF transfer film before applying it to a garment. It is usually done by heating the transfer film in an oven or under a heat press. This crucial step activates the adhesive, ensuring proper bonding during heat pressing.
Proper curing solidifies the printed design on the film (without fully applying it to fabric just yet) so that it can later be heat-pressed onto a garment.
Pre-Pressing
Pre-pressing is when you briefly press a garment (usually for 5–10 seconds) before applying a transfer to remove moisture and wrinkles.
Pre-pressing ensures a flat, dry surface, which helps the DTF transfer adhere more evenly. It can also prevent issues like steam or moisture from interfering with the bond.
Post-Pressing
Post-pressing is an optional second heat press done after removing the transfer film. This additional press improves durability and removes excess gloss from the finish.
For example, once the carrier is peeled off, you can cover the design with a Teflon or parchment sheet and press again for 5–10 seconds. This extra step helps embed the design into the fibers and can matte down any glossiness, ensuring the print is well sealed (many do this to “draw the vinyl further into the fabric” for better hold).

DTF Equipment & Materials
Using the right equipment and materials is essential to achieving consistent and high-quality prints. DTF printing involves a combination of specialized printers, heat presses, adhesive powders, and processing software. This section covers essential components of the DTF printing workflow.
DTF Printer
A DTF printer is a specialized inkjet printer (often a modified desktop or wide-format printer) that deposits textile pigment inks onto PET film in high resolution. DTF printers use Cyan, Magenta, Yellow, and Key (CMYK) inks plus white ink to produce full-color transfers. These printers usually work in tandem with software to manage color and quality.
PET Film (Transfer Film)
PET film is a special type of transfer film. It is a clear polyester-based transparent sheet that holds the printed design before DTF prints are transferred onto fabric. The design is printed on this film and coated with adhesive powder. The PET film endures the heat press and then is peeled away, leaving the design on the garment.
Heat Press Machine
A heat press machine applies heat and pressure to transfer a design from film to fabric. It uses a heated platen (metal plate) and pressure to apply transfers to garments. In DTF, a heat press is required to marry the printed, powdered film to the fabric at a specific temperature, time, and pressure.
Platen
Platen refers to the flat, heated plate on a heat press that comes into contact with the transfer. The bottom platen usually holds the garment, while the top platen provides heat and pressure. A quality platen distributes even heat for consistent transfers.
Hot Melt Adhesive Powder
Hot melt adhesive powder is a fine thermoplastic powder (often polyurethane-based) that is applied to the wet ink on the DTF film, acting as the glue for the transfer. When heated, this powder melts and bonds the design to the fabric.
The adhesive powder is what gives DTF transfers strong adhesion to various materials (cotton, polyester, blends) once heat pressed. Hot melt adhesive powder is available in fine, medium, and coarse grades for different textures and adhesion strengths.
RIP Software (Raster Image Processor)
The raster image processor (RIP) software is used to manage color layers, ink density, and white ink settings for DTF printing. It controls color profiles, ink levels, and print layouts to manage the printing parameters for DTF jobs and help ensure the design prints correctly onto the film.
Powder Shaker Machine
A powder shaker machine is an automated machine that evenly applies and recycles hot-melt powder onto DTF films. Instead of manually sprinkling adhesive powder, a powder shaker uniformly coats the printed film with adhesive.
It often has a built-in heater to begin the curing, which improves consistency and reduces any leftover mess.
Curing Oven (Tunnel Dryer)
A curing oven or tunnel dryer is a heating device (conveyor tunnel oven or countertop dryer) that melts and cures the adhesive powder on the printed film. After the DTF printer applies ink and powder, the film passes through the curing oven to fuse the powder into a solid glue layer in preparation for heat pressing.
Protective Cover Sheet
A protective cover sheet is a heat-resistant sheet (often Teflon or parchment) placed over a transfer and garment during pressing to protect both the garment and the heat press from direct contact. It helps distribute heat evenly and prevents any ink or melted adhesive from transferring to the press platen.
The protective cover sheet also helps prevent the scorching of sensitive fabrics.

DTF Ink & Adhesive Terms
The right ink and adhesive play a significant role in the quality and durability of DTF printing. These materials affect color vibrancy, print flexibility, and wash resistance. Understanding these terms will help you choose the best options for your printing needs.
DTF Ink
DTF inks are specially formulated, water-based inks made specifically for DTF printing. It produces vivid and flexible prints. They typically come in CMYK colors for the design and a separate white ink for opacity. These inks are designed to remain durable and stretchable after heat curing and transfer.
CMYK
CMYK stands for the four primary ink colors used in full-color printing: Cyan, Magenta, Yellow, and Key (Black). DTF printers use CMYK inks (plus white) to produce vibrant, opaque designs and blend virtually any color. The combination of these transparent inks on the transfer film produces the final image.
White Ink (Underbase)
White ink in DTF is heavy in pigment (titanium dioxide) and requires regular stirring or circulation to avoid settling. It’s absolutely essential for bold, visible designs on non-white materials.
White Ink Circulation System
A white ink circulation system is a feature in high-end DTF printers that prevents white ink from settling and clogging printheads.
Adhesive Powder Grades
- Fine: Smooth texture, used for detailed designs
- Medium: Versatile for most garments
- Coarse: Extra adhesion for textured fabrics like fleece
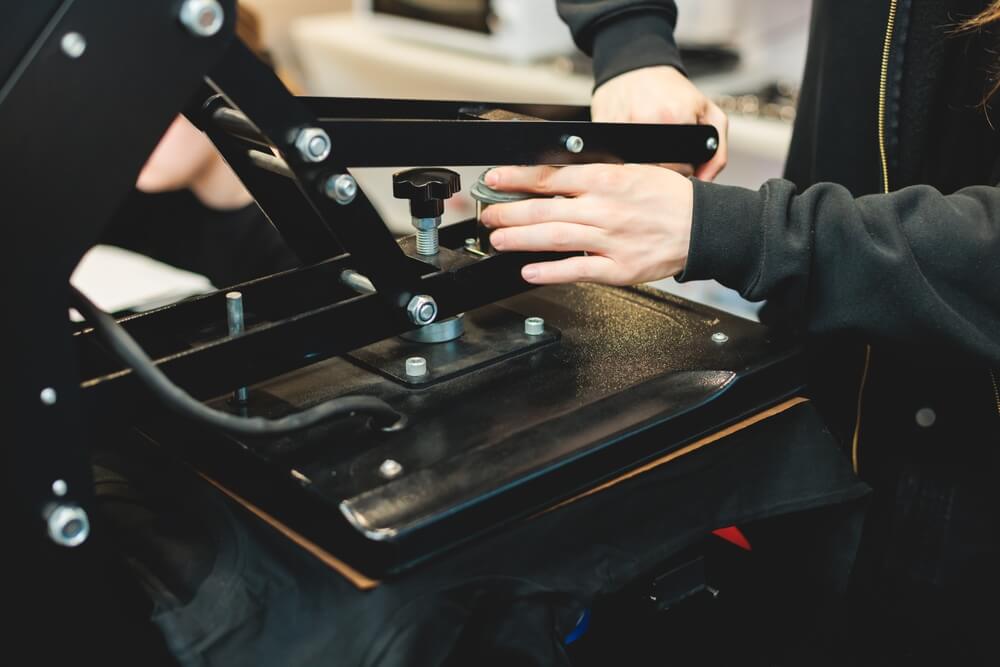
DTF Application Techniques
Applying DTF transfers correctly is key to achieving long-lasting and visually appealing results. This section covers the different application techniques, heat settings, and pressure requirements necessary for a successful transfer.
Hot Peel
Hot peel is a transfer application method in which you peel off the film immediately after pressing while it’s still hot.
Hot peel transfers allow for quick workflow since you don’t have to wait for cooling. The downside is that you must peel carefully to avoid lifting the still-warm print.
Cold Peel
A cold peel transfer method is when the film carrier is left on the garment until it cools down completely before removal. Cold peel is often preferred for very detailed designs or when maximum adhesion is needed, as letting the transfer cool stabilizes the print. Only peel the film off once it’s cool to the touch.
Warm Peel (Easy Peel)
This is a flexible application approach. Depending on the product’s instructions, the transfer can be peeled either while warm or after cooling. These “easy peel” transfers offer a balance — you might wait just a few seconds after pressing (not fully cold) to peel, mixing the speed of a hot peel with the safety of a cold peel.
Pressing Temperature & Time
- Cotton: 310°F (155°C) for 15 seconds
- Polyester: 285°F (140°C) for 10-12 seconds
Pressure Settings
- Light Pressure: Soft hand feel, used for lightweight garments
- Medium Pressure: Standard for most transfers
High Pressure: Extra adhesion for textured fabrics

Common DTF Issues & Fixes
Even with the best equipment and materials, challenges may arise in DTF printing. This section highlights common issues DTF printers face and provides solutions to troubleshoot and improve print quality.
Print Head Clogging
Print head clogging occurs when dried ink or debris blocks the inkjet nozzles, leading to missing areas or streaks in the print. Frequent nozzle checks and head cleanings are needed to prevent clogs, especially since white ink in DTF can settle and clog more easily. Neglecting this can halt printing or cause gaps until the nozzles are cleaned.
Poor Adhesion (Peeling/Cracking/Flaking)
Poor adhesion occurs when the transferred design does not stick fully to the garment or later cracks and lifts off. This usually indicates an issue with the bonding.
Common causes are not enough adhesive powder, insufficient heat or pressure during pressing, or incompatible fabric treatment. The result is prints that may peel at the edges or flake after washing. Ensuring proper powder coverage and correct press settings (time/temp/pressure) resolves most adhesion problems.
Banding
Banding is a print defect where you see visible horizontal lines or streaks across the image. It can result from clogged nozzles, improper printhead alignment, or incorrect settings. Banding manifests as uneven color or faint lines in solid areas.
Regular maintenance and using the correct International Color Consortium (ICC) profile and resolution help minimize banding.
Ink Bleeding
Ink bleeding is where the ink spreads beyond the intended design boundaries, causing a blurry or fuzzy look. Excessive ink volume, incorrect curing, or low-quality film can lead to bleeding as the wet ink wicks or smears. To fix this, printers often reduce ink saturation in the RIP or improve the curing process so that the ink dries without spreading.
Smudging
Smudging or smearing in the printed design often results from the ink not drying properly on the film. If the printed film is touched or moved too soon, or if too much ink is laid down, the design can smudge. Proper curing (or using a quick drying setting) and handling the film carefully by the edges will help prevent smudges.
Color Inconsistency
Color inconsistency is when printed colors are uneven, shifted, or do not match the design. For example, prints look faded or have unpredictable hues.
This can result from poor ink mixing (especially white ink settling), a miscalibrated printer, or an incorrect color profile. The solution is to shake/stir inks (maintain white ink), calibrate the machine, and use correct ICC profiles so that colors remain accurate and vibrant.
Dye Migration
Dye migration is a problem mainly on polyester or richly dyed fabrics where the garment’s dye reactivates under heat and bleeds into the transfer ink. It often shows up as a color cast (e.g. white prints turning pink on a red polyester shirt) a day or two after pressing.
To combat this issue, DTF users employ lower pressing temperatures, use poly-blocking adhesive powder (or even special blocker base layers), and possibly increase the white under base opacity to block the fabric dye.

Wholesale Clothing & Business Terms
Understanding wholesale apparel options and ordering requirements is important when using DTF printing for your business. This section covers key business-related terms to help you source blank apparel efficiently.
Wholesale
Wholesale sellers sell goods in large quantities at lower per-unit prices, typically to other businesses rather than directly to consumers. In the apparel context, wholesale purchasing (e.g. buying shirts from ShirtMax) lets custom print shops or brands get blank garments in bulk at a discount, then decorate and resell them at retail prices.
Bulk Discounts
Bulk discounts are reduced pricing tiers or percentage discounts you get when buying a large number of items at once.
ShirtMax, for example, offers bulk discounts in addition to wholesale pricing, meaning the more blank apparel you buy in one order, the lower the cost per item — helping businesses increase their profit margins.
Blank Apparel (Blanks)
Plain, undecorated clothing, such as blank t-shirts, hoodies, or hats, is intended for custom printing or embroidery. These items come without designs or logos so that businesses (or crafters) can add their own artwork. ShirtMax specializes in blank apparel for screen printing, DTF transfers, sublimation, and more.
Cotton
Cotton is a natural fiber that is soft and breathable. It is commonly used in t-shirts and is valued for its comfort.
100% cotton garments print well with most methods (DTF, DTG, screen print) and are a staple blank apparel choice, though pure cotton can shrink if not pre-shrunk.
Polyester
Polyester is a durable, quick-drying synthetic fabric often used in performance or athletic wear. It is ideal for sublimation printing (since it readily bonds with dye-sub inks) and also works well with DTF transfers.
However, heat-pressing poly requires care to avoid dye migration and scorching, so lower-temperature transfers are often considered the safest option.
Cotton-Poly Blend
A cotton-poly blend is a fabric that combines cotton and polyester fibers (common ratios are 50/50 or 60/40). Blended shirts balance the comfort of cotton with the strength and lower shrinkage of polyester.
They are popular blanks because they are versatile – they can be used with DTF, screen printing, and other methods. Cotton-poly blends also tend to have less shrink and wrinkles than 100% cotton.
Tri-Blend
Tri-blend is a high-quality fabric that blends three fibers – typically cotton, polyester, and rayon. Tri-blend shirts are very soft and have a fashionable drape; they are a premium blank option. Printing on tri-blends is possible with DTF transfers, but the lower polyester content (and the addition of rayon) can affect vibrancy slightly (often giving off a vintage look).
Ring-Spun Cotton
Ring-spun cotton is a type of cotton fabric in which the fibers are continuously spun and twisted to create a finer, softer thread. Ring-spun cotton shirts have a smoother, more luxurious feel compared to regular carded cotton.
Many wholesale t-shirts (e.g., Next Level or Bella+Canvas brand) are ring-spun, which makes them great for retail-quality printing.
Pre-Shrunk
“Pre-shrunk” refers to fabric or garments that have been preliminary washed or heat-treated to minimize shrinkage after purchase.
Pre-shrunk shirts will still tighten a little over time, but not dramatically — this is a key selling point for wholesale blanks, as printers know the garment will retain its size after customers wash it.
Tear-Away Label
A tear-away label is a garment neck label or tag designed to be easily removed by tearing. Many wholesale blank shirts come with tear-away labels, so print shops can remove the manufacturer’s tag and replace it with a custom-branded label (or leave it tagless for comfort).
This is ideal for rebranding when you launch your own clothing line using blank wholesale apparel.
SKU (Stock-Keeping Unit)
A stock-keeping unit (SKU) is a unique code retailers and warehouses use to identify and track each product variant (style, size, color) in their inventory.
For example, each type of blank t-shirt on ShirtMax has its own SKU to manage orders and stock levels. In practice, an SKU is often an alphanumeric string that you’ll see listed for each item. It’s extremely useful for reordering specific products.
MOQ (Minimum Order Quantity)
Minimum order quantity refers to the smallest number of units a supplier is willing to sell in one order.
Some wholesalers require an MOQ (for instance, only selling in dozens or cases), but ShirtMax has no minimum order, which means you can buy even a single piece at wholesale pricing.
Understanding MOQ is important when planning purchases – a zero or low MOQ gives flexibility, whereas a high MOQ means a larger upfront investment.
Print-on-Demand (POD)
POD is a business model where products (like custom T-shirts) are produced only after an order is received rather than pre-printing large quantities. POD businesses often use DTF transfers or DTG printing on blank apparel to fulfill single orders in real time.
This model minimizes inventory cost and risk, making it a popular choice for online t-shirt businesses since you can list many designs and only print a shirt when a customer buys it.
Why Choose ShirtMax DTF for Your Wholesale Apparel Needs?
DTF printing offers unmatched versatility, durability, and efficiency for custom apparel. Whether you’re a small business or a high-volume shop, ShirtMax provides high-quality blank apparel ideal for DTF transfers at wholesale pricing.
- No minimum order requirements – Perfect for startups and growing brands.
- Bulk pricing discounts – Maximize profit margins on wholesale purchases.
- Extensive selection of blank apparel – From cotton tees to polyester performance wear.
- Fast shipping and fulfillment – So you can keep your business running smoothly.
Don’t settle for subpar results — take your DTF printing to the next level with premium wholesale apparel from ShirtMax.